Written by: Sudeshna Ghosh
Table of Contents
Introduction to AI in Capacity Planning
Leveraging Artificial Intelligence (AI) and Machine Learning (ML) for capacity planning is becoming increasingly pivotal for manufacturers. This innovative approach allows enterprises to comprehensively assess their operations, encompassing vital elements like schedules, workforce management, raw materials, and budgets. By integrating AI capacity planning into their strategies, manufacturers can optimize productivity, effectively manage production costs, and ensure resilience, particularly in the face of economic fluctuations.
This discourse delves into the transformative impact of AI on traditional manufacturing paradigms. It illuminates how AI equips manufacturers with predictive capabilities, streamlining processes, and a competitive edge, thereby cementing its status as an indispensable component in today’s ever-evolving market.
Book a demo to experience the meaningful insights we derive from data through our ai capacity planning analytical tools and platform capabilities. Schedule a demo today!
Request a Free DemoImportance of scaling AI in manufacturing Operations
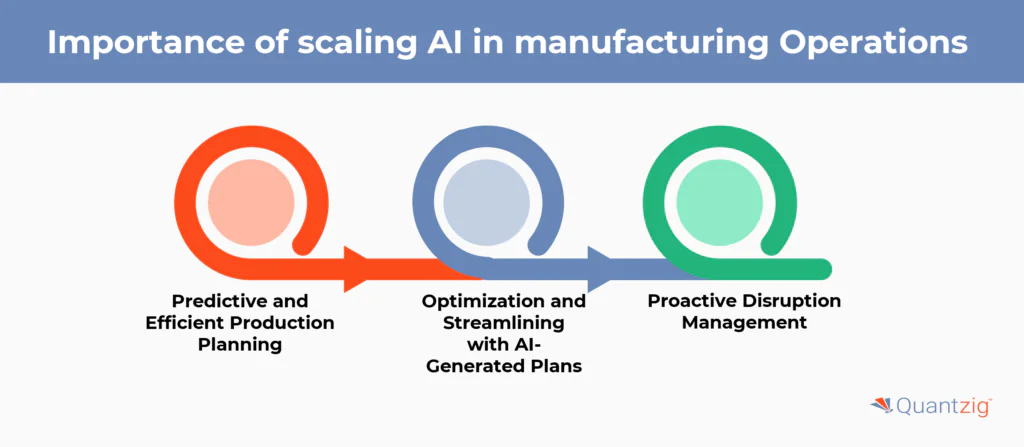
The significance of scaling Artificial Intelligence (AI) within manufacturing operations cannot be overstated in today’s rapidly evolving landscape. As consumer demand continues to fluctuate, manufacturers face the challenge of optimizing their production processes while effectively managing resources such as raw materials and costs. In this context, leveraging AI and Machine Learning (ML) becomes paramount for strategic capacity planning, resource management, and supply chain optimization.
By embracing AI-driven solutions, manufacturers can effectively navigate complexities, streamline operations, and gain a competitive edge in the market. Additionally, the integration of statistical algorithms and machine learning algorithms into IT operations and capacity planning processes further strengthens manufacturers’ capabilities to adapt to changing market dynamics and optimize their manufacturing resources. Through intuitive UI portals, manufacturers can harness the power of AI to make informed decisions and drive efficiency across their manufacturing resources, ushering in a new era of agile and adaptive manufacturing.
1. Leveraging AI for Predictive and Efficient Production Planning
The integration of AI into production planning represents a pivotal advancement in manufacturing. Leveraging historical data and external market influences, AI tools alongside machine learning algorithms facilitate precise predictions of future demand. Such foresight plays a critical role in enabling manufacturers to fine-tune inventory levels, minimize holding costs, and adeptly respond to customer demands. This innovative approach transcends traditional methodologies, empowering enterprises to optimize manufacturing resources and enhance their enterprise infrastructure.
Through strategic capacity planning guided by AI-driven insights, manufacturing companies can efficiently allocate resources, streamline IT operations, and bolster IT management practices. In essence, AI’s integration revolutionizes resource management in manufacturing, paving the way for heightened operational efficiency and sustainable growth.
2. Optimization and Streamlining with AI-Generated Plans
AI-generated prebuilt capacity and production plans leverage advanced statistical and machine learning algorithms to optimize manufacturing resources efficiently. By integrating with enterprise infrastructure and IT management systems, these plans offer seamless integration into existing workflows, enhancing operational efficiency across the board.
Capacity planning, coupled with resource management, enables manufacturing companies to allocate resources effectively, ensuring that production meets demand without overstretching resources or causing bottlenecks. Strategic capacity planning takes into account long-term business goals and market projections, aligning production capabilities with future growth opportunities.
3. Proactive Disruption Management
AI brings transformative benefits to manufacturing by proactively identifying and mitigating potential disruptions. Predictive analytics, a key feature of AI, can anticipate equipment failures, allowing for timely preventive maintenance and avoiding costly downtime. This predictive approach extends the asset lifecycle, reduces maintenance costs, and bolsters operational efficiency.
In a nutshell, the imperative of scaling Artificial Intelligence (AI) in manufacturing operations is undeniable, given its transformative potential in enhancing efficiency, resilience, and competitiveness. By leveraging AI and Machine Learning (ML), manufacturers can effectively navigate the complexities of fluctuating consumer demand and optimize their production processes and resources, including raw materials and workforce management.
Experience the advantages firsthand by testing a customized complimentary pilot designed to address your specific capacity planning requirements. Pilot studies are non-committal in nature.
Request a Free PilotChallenges in Manufacturing Without AI Capacity Planning
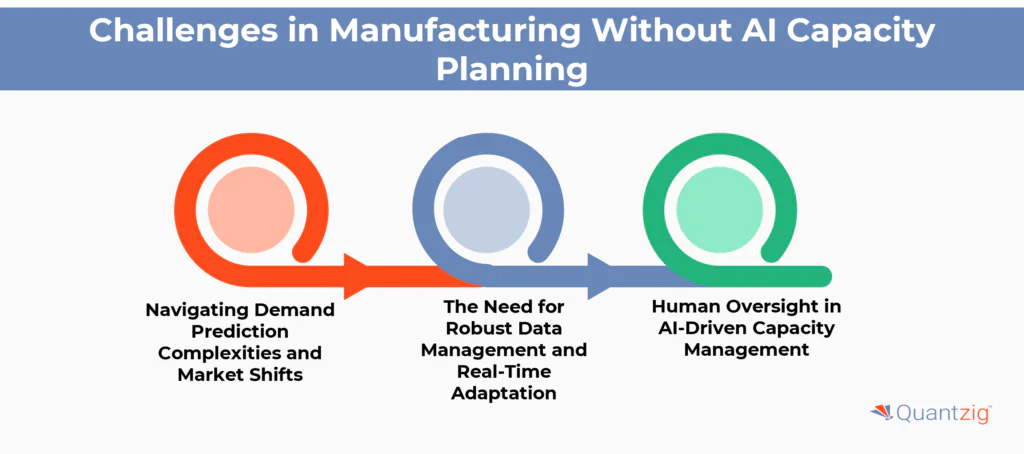
Manufacturing without AI (artificial intelligence) capacity planning poses formidable challenges across various fronts, including forecasting, optimization, resource allocation, demand management, and integration of the Internet of Things (IoT). Traditional methods struggle to predict demand accurately, leading to overproduction or missed opportunities. Without AI-driven techniques, efficiency remains suboptimal, hindering adaptation to market dynamics. Inefficient resource allocation and lack of legitimate data exacerbate these issues, while IoT integration remains underutilized. Aggregate planning also suffers, impacting production schedules and resource utilization. Output variability further complicates matters, necessitating flexible strategies. Some of the key challenges include:
1. Navigating Demand Prediction Complexities and Market Shifts
Even with AI assistance, predicting future demand remains a complex task, susceptible to unpredictable market shifts. This unpredictability can render forecasts less accurate, leading to challenges in aligning production with fluctuating demand. Without a robust AI system, manufacturers may face issues like overstocking or underutilization of resources, impacting cost efficiency and market responsiveness.
2. The Need for Robust Data Management and Real-Time Adaptation
Accurate integration of historical data with market variables demands a strong data collection and management system, often necessitating significant investments. Generating contingency plans and adapting to complex production dynamics require a deep understanding of manufacturing processes and real-time operational adjustments.
3. Human Oversight in AI-Driven Capacity Management
While AI and automation enhance efficiency, human intervention remains essential for contextual understanding and nuanced decision-making. Human oversight in validating AI-generated recommendations ensures a balanced approach, considering factors beyond data, such as market trends and strategic considerations. This synergy between AI’s predictive capabilities and human judgment minimizes costly errors and optimizes capacity planning.
Get started with your complimentary trial today and delve into our platform without any obligations. Explore our wide range of customized, consumption driven analytical solutions services built across the analytical maturity levels.
Start your Free TrialIn conclusion, the integration of AI capacity planning is not just advantageous but imperative for modern manufacturing. With the dynamic nature of consumer demands and market fluctuations, traditional methods fall short in providing accurate demand forecasts and efficient resource allocation. By leveraging optimization models driven by AI algorithms, manufacturers can streamline operations, minimize waste, and maximize output. Additionally, the utilization of legitimate data and IoT integration enables real-time insights and informed decision-making, essential for staying competitive in the industry.
Transformative Advantages of AI-Driven Strategies
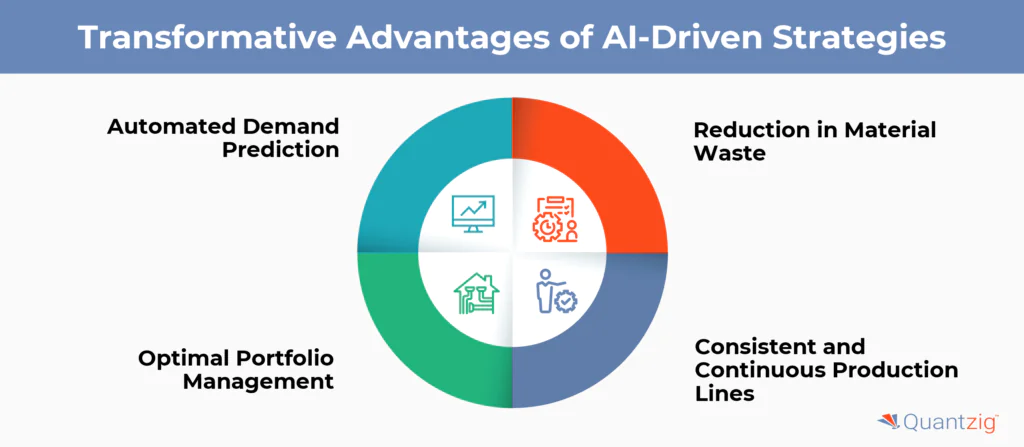
AI-driven strategies facilitate efficient IT operations and capacity planning processes, optimizing resource allocation and enhancing overall performance. From root-cause analysis to the creation of insightful data visualizations, these strategies empower decision-makers to gain valuable insights into their operations, enabling proactive decision-making and fostering innovation. As manufacturing companies embark on their journey towards digital transformation, the adoption of AI-driven strategies emerges as a cornerstone for achieving sustainable growth, production capacity, and competitive advantage in today’s data-driven world. AI Capacity Planning is revolutionizing the manufacturing industry by offering three core benefits:
1. Automated Demand Prediction:
AI’s sophisticated data analysis capabilities enable manufacturers to accurately forecast demand. This automation minimizes overproduction and shortages, aligning production more closely with market needs.
2. Reduction in Material Waste:
By fine-tuning production based on precise demand forecasts, AI significantly reduces material waste. This not only optimizes asset load and work orders but also contributes to sustainability initiatives.
3. Optimal Portfolio Management:
AI-generated optimal portfolio plans align production capacities with market demand. This ensures operational efficiency, reduces downtime, and supports a lean manufacturing approach.
4. Consistent and Continuous Production Lines:
Integrating AI in resource capacity planning is vital for a retail company to effectively manage fluctuating sales demands. By analyzing customer demand patterns and employing AI algorithms, the company can optimize server capacity and compute environments according to changing demand trends. This proactive approach transcends the limitations of traditional capacity planning by facilitating swift capacity adjustments based on application performance and evolving instance types.
AI-driven capacity planning in manufacturing is revolutionizing resource planning and capacity strategy by leveraging predictive analytics for precise demand forecasting and cost optimization. Unlike traditional capacity planning, AI facilitates continuous improvement in IT operations and aligns with technology advancements to meet fluctuating customer demand. The future of AI in capacity planning promises unparalleled efficiency and responsiveness, driving the next era of manufacturing excellence.
The Transformative Impact of AI Capacity Planning in Manufacturing
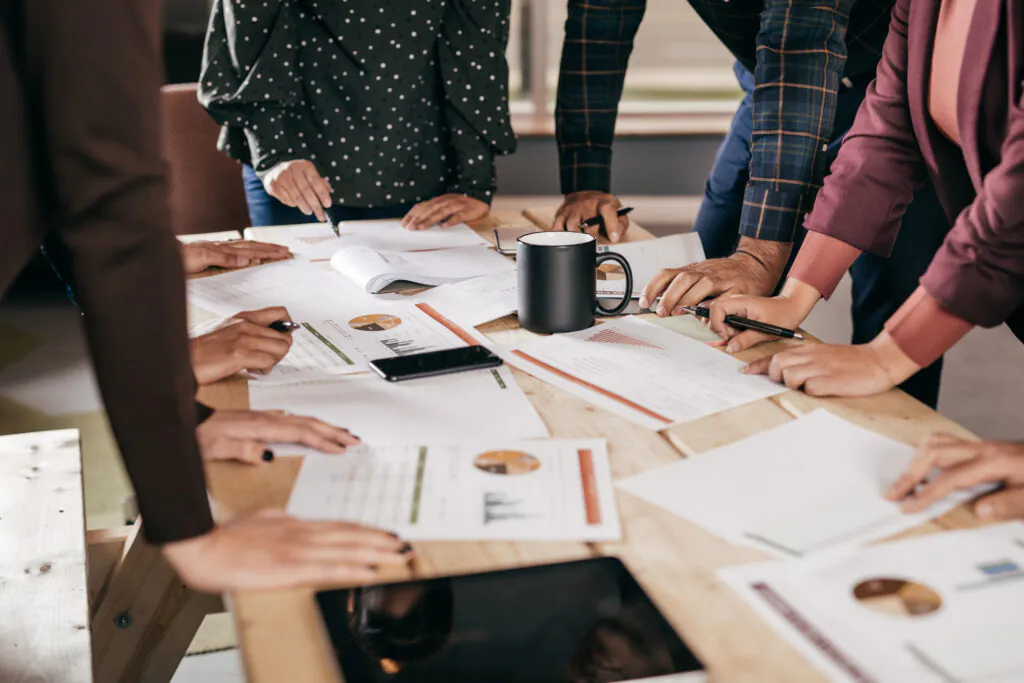
By harnessing a combination of Machine Learning (ML) algorithms, statistical-probabilistic algorithms, and simulation algorithms, AI (artificial intelligence) capacity planning enables manufacturers to analyze telemetry data from their physical IT infrastructure and compute environments. Through strategic predictive capabilities, organizations can optimize resource allocation, identify capacity requirements, and proactively address potential security intrusions and performance issues. Additionally, AI facilitates the creation of data visualization dashboards, providing insights into baseline norms and capacity adjustments across hybrid environments. Key aspects of this transformation include:
1. Alignment with Market Needs:
Automated demand prediction allows manufacturers to produce in line with actual market requirements, reducing the likelihood of overproduction and shortages. This not only enhances brand image by demonstrating responsiveness to customer demands but also fosters stronger relationships with stakeholders.
2. Sustainability and Resource Optimization:
The reduction of material waste through AI’s precision not only conserves resources but also aligns manufacturing practices with sustainability goals. By leveraging resource planning software and modern AI-driven techniques, manufacturers can mitigate environmental impact while maintaining operational efficiency.
3. Enhanced Operational Productivity:
AI-driven optimal portfolio plans ensure that AI for Manufacturing processes are both efficient and responsive, reducing downtime and enhancing productivity. This eliminates the time-consuming and error-prone nature of manual capacity planning, enabling quicker project planning and greater adaptability to changing demands. Additionally, it addresses the lack of responsiveness inherent in traditional methods, ensuring that production capacity plans are aligned with market needs.
These advantages culminate in streamlined, cost-effective, and environmentally conscious manufacturing operations. AI Capacity Planning empowers manufacturers to navigate the ever-changing global market landscape confidently, leveraging predictive insights to inform strategic decision-making and achieve operational excellence.
By integrating AI (artificial intelligence) and Machine Learning (ML) algorithms, manufacturers can optimize processes, ensuring that production aligns precisely with consumer demand and minimizes missed opportunities. Through accurate data analysis, AI-driven techniques, and advanced analytics, manufacturers can optimize resource utilization, improve inventory availability, and meet market demand efficiently. This proactive approach not only enhances Return on Investment (ROI) but also fosters a proactive and sustainable approach to manufacturing, ensuring the long-term success of enterprises across various industries and operational levels.
Conclusion:
In conclusion, AI capacity planning emerges as an indispensable strategy for manufacturers seeking to optimize performance and scalability in the ever-evolving business landscape. By integrating AI (artificial intelligence) and Machine Learning (ML) algorithms, manufacturers can strategically align their production capacities with the dynamic fluctuations of consumer demand, thereby minimizing missed opportunities and maximizing Return on Investment (ROI). This proactive approach, supported by accurate data analysis and advanced analytics, enables manufacturers to anticipate market fluctuations, optimize production schedules, and identify bottlenecks within the supply chain.
As the future of AI in capacity planning unfolds, it promises to revolutionize traditional approaches, offering innovative solutions to the intricacies of production capacity planning and resource allocation. With AI-driven predictive models and monitoring capabilities, manufacturers can make informed decisions, enhance performance, and thrive in a competitive business landscape, thereby ensuring the success and sustainability of their enterprises.