Struggling to optimize your production capacity while reducing costs? In the fast-paced world of manufacturing, understanding production capacity is crucial to maintaining operational efficiency and profitability. Quantzig’s ERP capacity planning solution, powered by advanced data analytics, enables businesses to balance workloads, refine scheduling, and optimizing production with ERP resources. The result? Increased profitability, higher customer satisfaction rates (CSAT), enhanced resilience, flexibility to adapt to demand fluctuations, and smarter medium-term investment decisions.
With over 20 years of experience, Quantzig helps businesses enhance efficiency by tailoring cutting-edge planning solutions using capacity planning tools in ERP to specific production lines, categories, and sites.
Book a demo to experience the meaningful insights we derive from data through our analytical tools and platform capabilities. Schedule a demo today!
Request a Free DemoTable of Contents
Benefits of Using Quantzig’ s ERP Capacity Planning Services for your Business
Quantzig’s offerings are designed to streamline operations, enhance resource utilization, and improve adaptability across manufacturing systems. Our framework targets four critical components
Benefits
- Cost Determination Analysis: Evaluates factors influencing unit costs, such as pallet holding, waste risk, and binding expenses, ensuring more accurate pricing and financial planning. By reducing waste risk by 15%, Quantzig helped a leading food producer save $300,000 annually.
- Demand Levelling Module: Harmonizes product demand to reduce costly variations and manage uncertainties. A beverage company cut overproduction by 20%, reducing storage costs by $500,000 per year.
- Automation: Automated scheduling optimization reduces manual intervention and accelerates decision-making. A textile manufacturer cut scheduling times from 2 days to just 4 hours, improving production line efficiency by 18%.
- Scheduling Optimization: Efficiently sequences manufacturing and packaging activities, cutting labor costs, waste, and changeover durations. A packaging company saw a 10% reduction in labor costs and a 15% decrease in changeover times.
By leveraging real-time, machine-generated data from production environments, businesses using Quantzig’s ERP platform gain immediate insights, improve decision-making, and implement changes on the go.
Real-Life Success Story: Food and Beverage Retailer in the UK
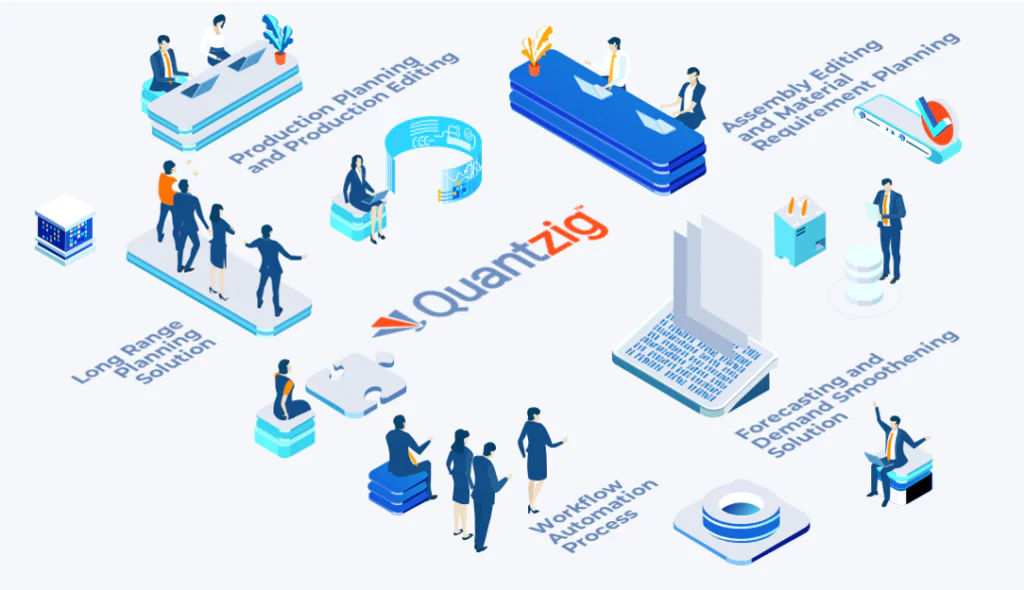
Client Problem:
A leading food and beverage retailer in the UK, with over 200 stores, faced significant challenges managing fluctuating demand across various locations. The complex production process, driven by specific recipes and variations, led to surplus production in some areas and shortages in others, resulting in overstocking worth $1.5M and underproduction losses of $800,000 annually.
Quantzig’ s Solution:
Quantzig implemented an advanced ERP capacity planning solution that acted as a centralized hub for managing capacity and production, material planning, and scheduling. The solution integrated seamlessly with SAP, allowing users to interact, forecast, and update production plans efficiently.
Modules such as the Production Simulator, Bill of Materials (BOM) Calculator, and Automated Scheduling Tool reduced the need for manual interventions while improving accuracy in forecasting and production timelines.
Impact:
- Reduced planning time from 3 weeks to 2 business days.
- Improved inventory levels by 25%, optimizing storage costs and reducing overstock by 20%.
- Boosted capacity utilization from 70% to 90%, driving a $500,000 reduction in operational costs.
Experience the advantages firsthand by testing a customized complimentary pilot designed to address your specific requirements. Pilot studies are non-committal in nature.
Request a free pilotWhat is ERP Capacity Planning?
This approach determines how well your company’s existing resources—labor, equipment, and materials—can meet production goals. It assesses available capacity against workload demand, identifying bottlenecks and improving resource allocation and scheduling.
For instance, a U.S. furniture manufacturer facing seasonal demand spikes used Quantzig’s planning platform to optimize raw material procurement, saving $600,000 in potential lost revenue.
Types of ERP Capacity Planning:
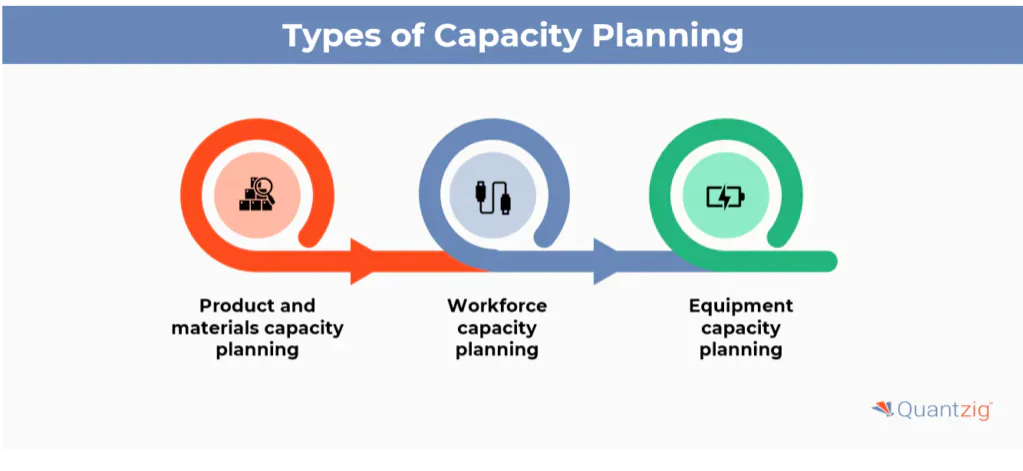
- Materials Capacity Planning: Ensures the availability of adequate raw materials. Example: A chemical manufacturer secured a 15% surplus in critical materials to avoid $200,000 in production delays caused by supplier shortages.
- Workforce Capacity Planning: Ensures enough labour is available to meet production needs. Example: A car manufacturer avoided $1M in production losses by pre-emptively scaling its workforce during peak demand.
- Equipment Capacity Planning: Identifies necessary tools and machinery to meet projected demand. Example: A global electronics company expanded its production lines, increasing equipment capacity by 25% to meet rising demand, leading to a $1.5M revenue increase.
Common Challenges in ERP Capacity Planning
While ERP optimization delivers major gains, many manufacturers face hurdles like unpredictable demand and fragmented data systems. A fashion brand misread winter clothing demand, ending up with $500,000 in excess inventory. After implementing Quantzig’s forecasting module, they cut forecast errors by 18% and reduced surplus stock by 10%.
Siloed data is another issue. When vital insights like equipment status or material shortages are spread across systems, it slows decisions. Quantzig resolves this with a unified platform for more effective capacity planning optimization.
Strategies for Successful ERP Capacity Planning
To combat these challenges in inventory and capacity planning ERP, manufacturers adopt different capacity planning strategies to improve production efficiency with ERP:
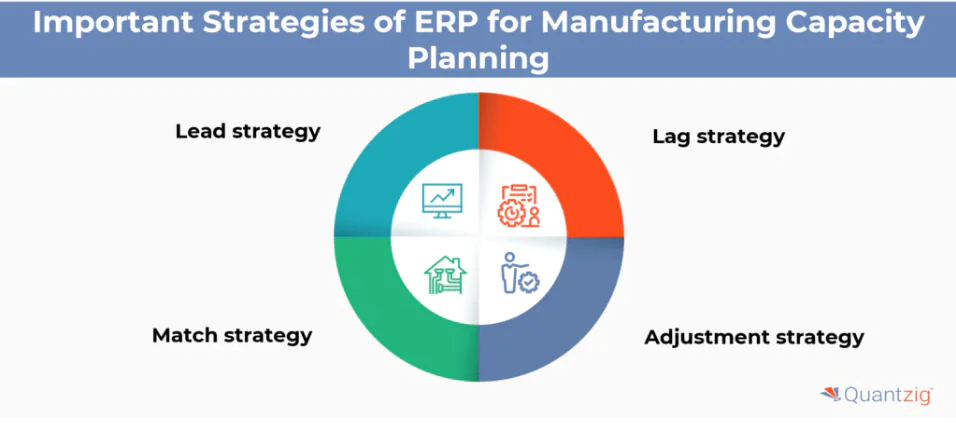
- Lead Strategy: Expands capacity ahead of projected demand. Example: A tech manufacturer adopted the lead strategy, adding two new production lines in anticipation of high product demand. This proactive move resulted in a $2M increase in market share.
- Lag Strategy: Adds capacity only when demand reaches maximum utilization. Example: A furniture company avoided overinvestment by using the lag strategy, expanding its workforce only after reaching 95% utilization, saving $500,000 in potential excess labour costs.
- Match Strategy: Gradual adjustments to capacity based on demand trends. Example: A pharmaceutical company used match planning, expanding manufacturing incrementally based on historical data, improving production efficiency by 15%.
- Adjustment Strategy: Relies on sophisticated forecasting tools to fine-tune capacity planning. Example: A food packaging company employed adjustment planning to align production with seasonal demand surges, increasing production efficiency by 20%.
Ready to Maximize Your Operational Efficiency?
Unlock the full potential of your manufacturing capabilities with Quantzig’s ERP capacity planning solutions. Don’t let inefficiencies hold you back—Reach out to our experts today and get started now to drive growth with smarter, data-driven decision-making.
Start your free trialBest Practices for ERP Capacity Planning
Define Capacity Requirements: Assess current and future production needs.
Example: A large dairy producer forecasted a 10% rise in demand during the holiday season, expanding production by 12% to ensure no stockouts.
Evaluate Current Capacity: Ensure resources are used efficiently.
Example: A steel manufacturer identified underutilized machinery, increasing capacity by 8% without additional investment.
Develop a Future Plan: Scale operations when necessary.
Example: A consumer goods company added two new manufacturing plants to meet projected growth, improving delivery timelines by 15%.
What unleashing Strategy can do for your Business:
With effective ERP capacity planning, businesses can:
- Reduce costs: A Canadian auto parts manufacturer reduced operational costs by $700,000 by optimizing raw material purchases.
- Ensure timely deliveries: A European electronics company maintained on-time deliveries for 99% of orders by synchronizing production capacity with customer orders.
- Prevent stockouts: A food processing company reduced stockouts by 25% by aligning supply with demand, increasing revenue by $400,000.
Conclusion
ERP Capacity Planning is a strategic lever for manufacturing success. By accurately forecasting demand, optimizing resources, and eliminating bottlenecks, businesses can drive profitability, improve operational efficiency, and enhance customer satisfaction. Quantzig’s advanced enterprise resource planning capacity offers the tools needed to align production capabilities with business goals, delivering tangible results like increased capacity utilization, reduced lead times, and optimized costs.
Don’t Wait—Start Optimizing Today!
The constantly evolving industrial landscape of ERP production planning, embracing digital ERP capacity management is no longer optional—it’s essential for long-term growth and competitiveness.