Written By: Priscilla Annoussamy
Companies now have even more reason to be concerned about the smooth flow of their goods. There is a growing focus on Sustainability and ESG compliance by consumers with the brands they engage with. Retailers and CPGS are driving transformation programs to ensure sustainability in all their operations from sourcing, processing, packaging and distribution and reverse logistics processes.
These days, environmental, social and governance (ESG) compliance is putting supply chains under pressure too.
What is ESG compliance? ESG compliance refers to the understanding of the ESG guidelines mandated by governmental and regulatory bodies, and the act of implementing them in internal policies and practices. It also involves the adherence to global frameworks and standards that guide toward sustainability. This way, companies can better demonstrate their credibility as a responsible and sustainable brand on the market.
All of this creates a complex and fast-moving landscape for any company looking to ship goods across borders. They must ensure their supply chains meet this set of new standards, potentially facing penalties and taxation if they don’t. In addition to all this, they must track and report their efforts correctly too.
Here are three key steps that will help companies to navigate the changing ESG trade landscape:
- Establish ownership
- Understand your supply chain end-to-end
- Set yourself up for continuous improvement
Don’t miss out on this vital resource – read on to revolutionize your product manufacturing practices and propel your business to new heights!
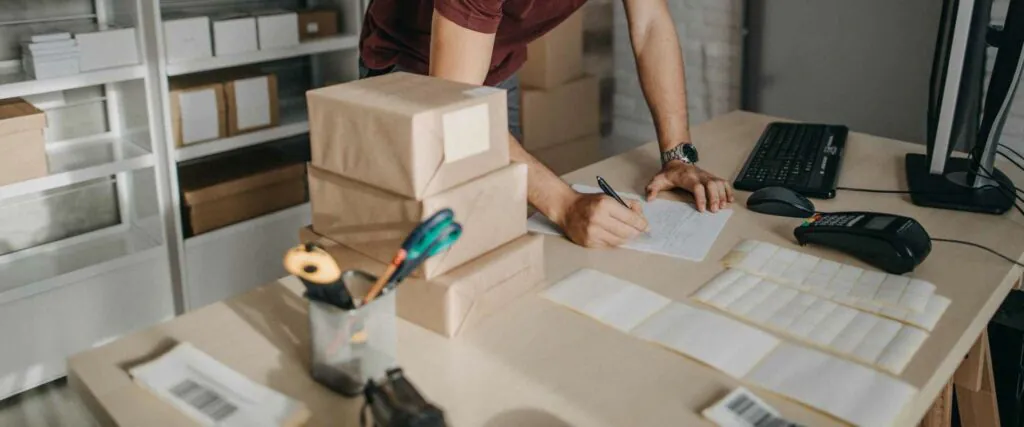
Table of Contents
Importance of building a strong compliance policy
Building a strong compliance policy is of utmost importance for companies, as it establishes the foundation for an efficient and effective governance framework. By implementing a robust compliance policy, organizations can ensure adherence to legal and regulatory requirements, mitigate risks, and safeguard their reputation.
First and foremost, companies must prioritize the establishment of clear and comprehensive policies and procedures. These guidelines serve as a roadmap for employees, outlining expected behaviours and actions in line with legal and ethical standards. By providing employees with a clear framework, companies can minimize the risk of non-compliance and promote a culture of integrity. Additionally, companies need to invest in regular training and education programs to keep employees informed about evolving regulations and best practices. By fostering a culture of continuous learning, organizations can empower employees to make informed decisions and act in accordance with compliance requirements.
Furthermore, companies should implement robust monitoring and reporting mechanisms to detect and address any potential compliance breaches. This includes conducting regular audits, implementing internal controls, and establishing channels for employees to report concerns or violations confidentially. A strong compliance policy also involves establishing a system of accountability and consequences for non-compliance. By enforcing disciplinary actions for violations, companies demonstrate their commitment to upholding ethical standards and deter future misconduct.
Building a strong compliance policy is essential for companies to ensure legal and ethical conduct, mitigate risks, and protect their reputation. By establishing clear policies, providing ongoing training, implementing monitoring mechanisms, and enforcing accountability, organizations can create a culture of compliance that fosters trust, integrity, and long-term success.
Mapping of your supply chain network
Identify your suppliers, manufactures, distributors and retailers. Once you have done this, you can identify the different stages of the process and the various transportation methods employed. As you map the supply chain, it is important to assess the compliance risks and sustainability implications at each stage. This includes being aware of potential risks such as disruptions, environmental impact and forced labour practices.
Secondly, you’d want to be able to retrace your steps so it’s important to track and record data at every stage of the process.
Thirdly, identify and collect sustainability-specific data. This involves mapping out relationships among facilities, suppliers, materials, finished goods, purchase orders and more to identify contingencies and risk exposure. Audit data for suppliers and facilities is also crucial, along with metadata to verify the authenticity of claims and certifications.
Digitize supplier information
- Digitizing supplier information is a crucial step in optimizing supply chain management. By capturing and storing data at every stage of the supply chain, businesses can gain valuable insights for quality control, risk management, and sustainability reporting. This process enables organizations to enhance operational efficiency, mitigate potential risks, and demonstrate their commitment to sustainable practices.
- By implementing robust digital systems, businesses can streamline the collection, analysis, and utilization of supplier data. This allows for real-time monitoring of product and material movements, ensuring transparency and traceability throughout the supply chain. With accurate and up-to-date information readily available, businesses can make informed decisions, identify areas for improvement, and proactively address any issues that may arise.
- Furthermore, digitizing supplier information facilitates effective quality control measures. By tracking product and material data, businesses can identify patterns, detect anomalies, and implement corrective actions promptly. This not only ensures consistent product quality but also enhances customer satisfaction and loyalty.
- Moreover, the digitization of supplier information enables comprehensive risk management. By analysing data related to suppliers, materials, and processes, businesses can identify potential risks and develop proactive strategies to mitigate them. This includes monitoring supplier performance, assessing compliance with regulations, and identifying alternative suppliers to minimize disruptions.
- Lastly, digitized supplier information plays a vital role in sustainability reporting. By tracking and analyzing data on suppliers’ environmental practices, resource consumption, and waste management, businesses can measure their environmental impact and identify opportunities for improvement. This enables organizations to align their operations with sustainable practices, meet regulatory requirements, and enhance their reputation as responsible corporate citizens.
- Digitalizing supplier information is essential for optimizing supply chain management. By leveraging digital systems to track products and materials, businesses can enhance quality control, mitigate risks, and demonstrate their commitment to sustainability. This data-driven approach empowers organizations to make informed decisions, improve operational efficiency, and maintain a competitive edge in today’s dynamic business landscape.
Structure the data to meet regulatory requirements
Finally, identify the laws and regulations that apply to your specific industry, products and regions. This can be done by conducting research, consulting with legal experts, and monitoring for regulatory updates.
Once the applicable laws and regulations have been identified, assess your compliance requirements, including the specific supply chain data needed for compliance. With the parameters in hand, it’s then your responsibility to track the data, while developing policies and procedures that enforce compliance.
Progress toward traceability takes time, but it works. Sustainability is a journey and we’re not yet at our destination. Compelled by regulation to forge a more sustainable future, brands are finding that traceability is not only good for the planet, but also for them.
How do you ensure sustainability compliance in an organization?
Sustainability compliance requires measurement and corrections at every single point of network operations and at every stage of the supply chain network. It becomes even more difficult for the processes involving stakeholders, partners, manufacturers, distributors and planners. The resolution is usually a combination of programs to create awareness and an efficient analytics roadmap to measure and control the processes.
It’s always better to be as proactive as possible regarding regulatory compliance but staying ahead of the curve and planning is difficult to do while running multiple programs and conducting business as usual. Luckily, there are trends in regulation policy, and one you can safely bet on is sustainability as a massive influence.
Success Story
Client Details
A leading F&B retailer in Canada
Challenges faced by the client
Frozen food is one of the key categories for the client. The current process of the client involved sourcing farm produce from a network of farmers. The challenge they were encountering with the current process was putting in place a compliance check management system. They were running into issues in ensuring that the chemicals used for pest control and soil ploughing were properly handled by the farmers. This was a key compliance that had to be measured and optimized at their sourcing.
Solutions offered by QZ
Quantzig had come up with an automation and process engineering solution to devise the ideal process control by enabling self-compliance for Farmers through a purpose-built mobile app that serves as a process check in addition to acting as an advisory to farmers in identifying their ideal proportion mix of chemicals that has a minimum environmental impact quotient (EIQ).
Impact delivered
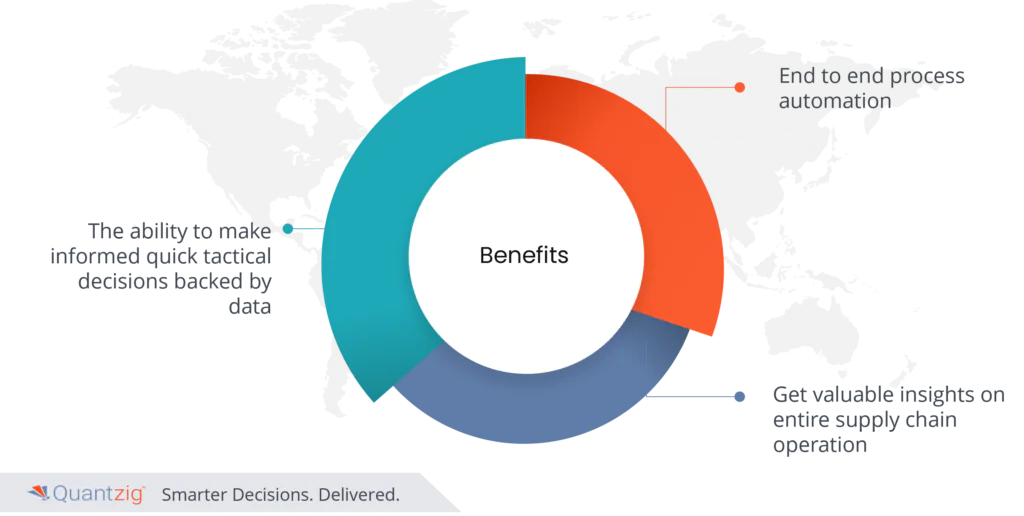
- The ability to make informed quick tactical decisions backed by data
- End to end process automation
- Get valuable insights on entire supply chain operation
Request a free proposal to understand how.
Read this article to know : Benefits of Purchase Order System for Your Organization